Battery_ZERObase
[반도체 공정] 3. Photolithography process (포토 공정) 본문
김성호 교수님의 <기초반도체공정> 유튜브 강의를 정리한 내용에 삼성 반도체 뉴스룸, SK 하이닉스 뉴스룸, 딴딴's 반도체사관학교, NNFC 종합실무과정 교육 내용 참조하여 공부한 것임을 밝힙니다.
* Photolithography
: Photo Litho graphy = Photo(빛) + Litho(돌) + graphein(인쇄) = 빛을 이용한 인쇄 기법
=> 설계하려는 반도체 회로 정보로 만들어진 Mask와 규격화된 빛을 이용하여, Wafer 위에 회로 패턴을 전사시키는 공정
cf) Yellow room?
: Photo 공정이 이루어지는 공간은 항상 노란색인 이유?
= PR이 단파장의 빛에 민감하기 때문에, 장파장의 빛만을 이용한 조명을 사용하는 것!
< Photo Process >
[A. Track Process]
: 노광을 제외한 공정
: Wafer Edge만 맞추어 Align한 후, 공정 진행
: 모든 Plate 공정 이후에는 cooling 공정을 필요로 함! (약 23℃의 chill plate 이용)
ex) TEL 사의 ACT8 (8인치 공정)을 예시로 하자면..
한 쪽은 Spinner(PR coating, Develop..)와 Plate(Soft bake, Hard bake..)로 이루어 짐.
-> Spinner: Spin 시간, RPM, 분사 위치.. 조정
-> Plate: 온도, 공정시간, Vapor 뿌려주는 정도.. 조정
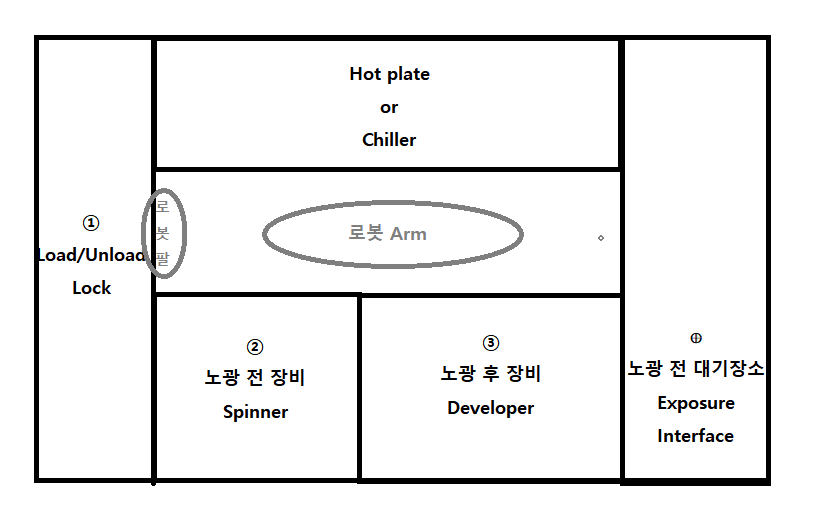
1. 접착제 (HMDS or BARC) 도포
: CD가 μm단위면 HMDS를 사용, nm단위는 BARC를 사용
* HMDS: PR을 표면에 잘 고정화해주기 위해서는 PR이 coating될 surface를 hydrophobic하게 변화시켜주는 과정
= Wafer Prime
1. Si Wafer는 native oxide 때문에 hydrophilic한 표면을 가지고 있음.
2. Cleaning 이후, HMDS를 이용하여 표면을 hydrophobic한 surface로 바꿔주는 wafer prime 과정을 거침.
->N2로 bubbling 후, gas상태로 wafer에 주입(100℃로 달궈진 plate 위에서)
* BARC: BARC가 빛의 반사를 방지과 동시에 HDMS의 접착 역할까지 수행
PR이 얇아질수록, PEB만으론 Standing wave effect을 해결할 수 없어 BARC 함께 사용
2. PR(Photoresist) 도포
: 균일한 PR 도포를 위해 Spin coating 진행
ㄴ> spin speed와 spin time을 조절하여 PR의 두께 결정
cf) PR(Photoresist)란?
-> 특정 파장의 빛을 쏘아주면 물리/화학적으로 변화가 일어나 성질이 변화는 유기물질
-> 주 성분은 Resin, 빛을 sensing 하는 첨가제로는 PAC(Photo Active Compound) 또는 PAG(Photo Acid Generator)
-> Etch나 이온주입 공정에서 Organic Barrier Mask의 역할 수행
-> 현상액에 대한 용해도가 변화 => 산염기 반응으로 제거
-> ① Positive PR: 빛을 조사한 부분이 develop 과정 이후 제거가 되는 PR, 사다리꼴 모양의 pattern 형성
pattern 해상도가 높으나, uniformity가 우수하지 못
② Negative PR: 빛을 조사하지 않은 부분이 develop 과정 이후 제거가 되는 PR, 역사다리꼴 모양의 pattern 형성
patter 해상도가 낮으나, 현상 시 swelling 현상이 발생
cf) Lift-off process: Negative PR 먼저 patterning 한 후, 직진성을 가지는 증착공정을 이용하는 방법
Etching을 하기 어려운 물질(noble metal[Pt]...)에 pattern을 새길 때 사용
but, 고온에서의 증착 공정을 사용해야 할 경우에는, PR이 고온에서 변형됨
: PR Coating 공정 순서
① Chuck으로 진공 잡아준 상태에서 Thinner를 먼저 뿌린 후, 빠르게 회전시켜 solvent 날려줌
(PR이 잘 퍼지도록 도와주기 때문에)
② 노즐 changer로 원하는 PR이 담긴 노즐을 선택 후, Arm1으로 센터 PR 코팅
(Spin 시간, RPM, 분사 위치 조정)
-> RPM을 줄이면 PR이 안으로 모이는데, RPM을 느리게/빠르게 하며 두께 조절 가
③ Arm2로 Thinner를 뿌려 테두리의 PR을 (+back rinse로 뒷면 PR도)제거하는 EBR 진행
-> but, chemical이라 약간 자국 남음
: PR profile
: PR 채택 시, 고려되는 지표
① PR의 용해성
② 민감도
③ 열적 안정성
④접합성
3. Soft bake
: PR의 90%에 해당하는 휘발성 물질(solvent)를 제거
: PR이 약간 단단해짐.
-> Track 기기에서 노광 기기로 넘어가기 전/후에, Stationary Buffer에서 Wafer가 대기
(최대한 대기시간 없도록 recipe를 짜는 게 가장 좋음!)
+ WEE(Wafer Edge Exposure)도 이 과정에서 진행 ( EBR 후에 남은 Edge의 자국을 UV로 다시 제거하는 공정
EBR보다 1mm정도 더 큰 영역 제거 )
[B. Exposure Process]
: 노광 공정
: Wafer의 flat/notch로 align을 진행
: 장비의 focus check (spec보다 벗어나면(±50nm), 0으로 다시 맞춰줌)
-> 공정마진이 0.1μm 이상이여야 정상이라 판단
4. Exposer (노광)
(1) Alignment process = 이전에 만들어진 pattern과 지금 만들려고 하는 pattern의 정렬 과정
flat/notch를 확인하여 align
+) Aligner: Mask를 Alignment key에 맞게 정렬한 후, 빛을 조사 (~1μm의 pattern까지 가능)
(2) Exposer process = PR이 반응할 수 있는, 파장이 짧은 UV 계열의 빛을 많이 이용
: Mask 전사 방법 = 1:1, 4:1, 5:1
-> stepper: pattern의 1/5 축소해서 웨이퍼에 투영
-> scanner: pattern의 1/4 축소 “
① Stepper: 빛 한 번에 도장처럼 꽝 찍으면서 pattern을 새기는 장비
but, lens의 중심부와 끝부분의 초점거리가 조금 다르다는 단점
-> 중심 부분과 가장자리 부분에 빛이 조사되는 정도가 달라서 수율 저하를 발생시킴
② Scanner: Wafer와 Mask를 움직여서, 초점이 잘 맞는 lens의 가운데 부분만 활용하여 빛을 조사할 수 있도록
-> Wafer과 Mask의 움직임을 잘 조정하는 것이 가장 중요!
cf) Twin Scanner?
: 노광기에 chuck이 2개 = measure side+exposure side
→ measure side scanner (wafer의 정보를 읽는 metrology)
→ exposure side (measure side에서 얻은 정보를 반영하여 노광)
cf) Photo Mask(Raticle)란?
-> 순도가 높은 석영(Quartz)을 가공해서 만든 기판 위에 Cr로 미세 회로를 형상화한 것
-> 투과형 Mask: I-line(365nm), KrF(248nm), ArF(193nm)를 포함하는 DUV에서 사용
반사형 Mask: EUV(13.4nm)에서 사용 (<- 단파장이라 대부분의 에너지가 마스크에서 흡수되기 때문에)
cf) 노광 Recipe에 입력해야 하는 것??
1) flat인지, notch인지?
2) Reticle size가 몇 인지?
3) Reticle의 어느 위치 Mask를 사용할건지?
4) Energy(->패턴크기), focus(->Resolution)
5) NA sigma(높을수록, Resolution 좋아지나, DOF 마진이 작아짐.)
6) 조명모드
7) Align key...
5. Post-Exposure Bake(PEB) 열처리
: PR을 굳혀줌으로써, 조사되는 빛의 Intensity가 고르게 되도록 해주는 공정
: 온도에 예민하기에, 다른 track 장비는 온도 sensor가 1개인 것과 달리 약 7개의 많은 sensor 보
cf) PEB 과정을 거치지 않는다면?
-> PR로 들어가는 빛과, 들어갔다가 반사되는 빛이 보강 및 상쇄 간섭을 일으키므로 PR에 조사되는
빛의 Intensity가 일정해지지 않는 Standing wave effect 발생
∴ 정상파의 영향으로 develop 과정에서 PR Profile side wall이 울퉁불퉁해지는 현상 발생!!
cf) PEB 대신, PR 아래에 빛의 반사를 막아주는 Anti-reflecting coating Layer(ARC)를 coating하는 방법도 있음.
6. Develop (현상)
: Wafer를 developer 용액에 담궈, 빛을 받지 않는 부분을 제거
① 원하는 위치를 지정하여 낮은 RPM으로 현상액을 도포
ex. (1000rpm 0.2s → 500rpm 1.5s → 100rpm 1.5s → 30rpm 3.0s)
② 현상될 동안은 38s 0rpm으로 정지(8인치 공정)
+) 12인치 공정에서는 현상 동안에도 고속회전 유지
③ 2000rpm으로 D.I water Rinse
7. Hard bake
: Etching process를 견딜 수 있도록, 남은 PR을 매우 Hard하게 굳혀줌.
너무 고온에서 진행할 시, PR이 녹아 변형이 되기 때문에 적절한 온도와 시간동안 진행해주어야 함.
8. Eching & PR strip
: Etching = PR을 Mask로 Etch 진행
: PR strip = 더이상 필요가 없어진 PR을 제거
방법 1. 유기용매 (Acetone 또는 Piranha(H2SO4:H2O2[1:1]))에 녹여 제거
but, 변형이 일어난 PR을 깨끗이 제거하는 데 한계, Piranha는 금속을 녹이기 때문에 금속인 경우 사용 X
2. PR remover 사용
3. O2 plasma ashing: O2를 이용해 만든 Plasma가 유기용매인 PR을 태움
but, PR residue가 남는다는 단점
9. Develop Inspect
① CD-SEM으로 CD 측정
1) Pre-Align (notch/flat)
2) pattern 관찰(노광 장비의 한계가 70nm라 가정하면, 70nm의 pattern부터 관측 가능할 것)
-> Line pattern: PR이 있는 pattern(-> CD측정, 70nm 목표 ±5%까지 허용)
-> Space pattern: PR이 없는 pattern
-> LWR(Line Width Roughness): LWR이 작을수록, 굴곡없이 이쁜 pattern 형성
② Overlay 측정
다섯 장소 정도를 지정해서 확인 -> 결과를 자동으로 노광 장비로 보내 보정되도록 함
ex. (X-transition, Y-transition, X-expansion, Y-expansion)
-> shot이 얼마나 shift/expansion 되었는지?
③ 현미경으로 Wafer 표면 측정
=> Focus는 장비 setting 초기에 맞추고 계속 사용
=> CD(노광장비 Energy)와 Overlay는 매일 측정 후 보정
* Photo 공정의 Issue
1. Resolution
: 얼마나 작은 크기의 pattern들을 그려낼 수 있는가?
: 빛의 회절 현상때문에, Mask에 빛을 조사하였을 때 원하는 영역보다 더 넓은 영역이 빛을 받음.
cf) Critical Dimension(CD): 만들어 낼 수 있는 최소한의 size (선폭...)
CD가 작을수록 미세화된 pattern 제작 가능
CD에 영향을 미치는 요소들은 다음의 관계를 가짐.
-> λ(빛의파장): 낮은 CD를 얻기 위해서는 짧은 파장의 빛을 사용해야 함.
파장이 짧은 빛을 사용하면 무조건 pattern 미세화가 가능하진 X
: DoF에 문제가 발생하기 때문!
cf) DoF(Depth of Focus) = 초점심도, 초점을 맞출 수 있는 range
파장이 짧아지면 초점을 맞출 수
있는 폭도 줄어든다는 단점
∴ 높낮이의 단차가 존재할 경우, 정확한 pattern 형성이 불가
=> DoF를 줄이기 위해, 평탄화 공정(Planarization Process)
+) 파장을 줄이지 않고도, CD를 줄일 수 있었던 이유??
=> 여러 공정 techniques로 인하여 가능!
① Phase Shift Mask(PSM): Pattern 간의 중첩을 방지하고자,
한 쪽에 빛의 phase를 바꿔줄 수 있는 물질을 도입하여 원하는 형태의 pattern을 얻을 수 있음.
but, 복잡한 pattern의 위상차 최적화 어려움 + 제작단가 ↑
② Immersion lithography: 매질의 굴절율(n)을 높여주고자
공기(n=1)가 아닌 물(n=1.44)을 사용하여 CD를 감소
③ Multi-patterning: 현상을 여러 번 진행하여 정교한 patterning
1. Double patterning: LELE...
2. Spacer patterning:
④ Opitical Proximity Correction(OPC): 공정 최종 결과를 보고,
실제 원하는 pattern에 가까워지도록 Mask를 보정
-> NA : Lens가 빛을 모아주는 능력, Lens의 크
2. Registration
: 각 Layer의 pattern들이 원하는 위치에 정확하게 정렬이 되어있는가?
3. Throughput
: 단위시간당 얼마나 큰 생산량을 보이는가?
cf) E-beam: 한 번에 빛을 쏘아주는 기존의 방식이 아닌, 전자를 하나씩 쏘아서 pattern을 형성하는 기술.
아주 미세한 pattern도 형성 가능하지만, throughput이 매우 좋지 않기 때문에 실제 사용되지는 X
'반도체' 카테고리의 다른 글
[반도체 공정] 4. Etching Process (식각 공정) (0) | 2023.07.12 |
---|---|
[반도체 공정] 1. 반도체란? 반도체 공정에 사용되는 기초 지식 (0) | 2023.07.08 |